Reproduction
Reproduction
The reproduction
Creating a reproduction of an antique doll
A stock of more than 300 head model molds and extensive documentation allow me to create reproductions.
The restoration part of my activity also provides me with valuable information.
Having very beautiful old dolls in my possession, I can make the most accurate shades and curves of the features (eyelashes, eyebrows, mouths…), specific to each manufacturer.
Manufacturing steps
1. The moulding process
Porcelain paste is a composition of earth (kaolin and feldspar) worked to have the consistency of pancake paste.
I pour it into the mold.
The plaster sucks in water and depending on the pause time, more or less thickness is fixed inside the mold.
Then I empty the mold to obtain a hollow part.
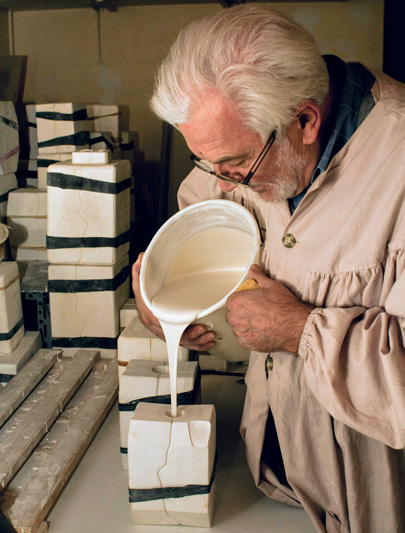
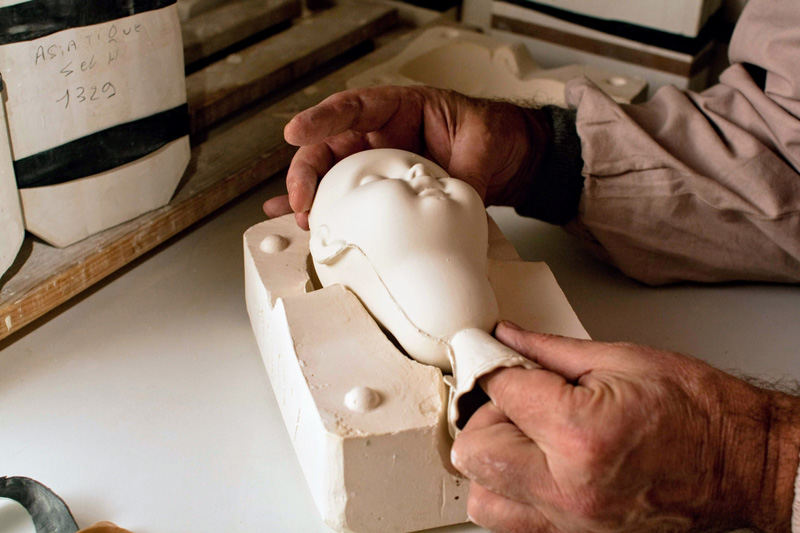
2. Demoulding, cutting, sanding
After the drying time, I remove the head from the mold and proceed to cut the cavity of the eyes, the top of the head, the neck and according to the models of the mouth (open or closed), the teeth…
To finish this step I make a scrubbing of the traces of separation of the mold, the part must have no defect because it would deform during firing.
3. Making of the porcelain biscuit
After a first firing at 800 degrees I obtain a soft ceramic piece on which I work on the finish: small retouches, sanding….
A second firing at 1300 degrees is made to obtain the porcelain biscuit (baked twice). At the exit of the furnace the part is reduced by about 20%.
For purists we should not say a porcelain doll because we don’t do enamelling like we do for crockery and we stay at the porcelain biscuit stage.
4. The coloration
Unless there is an exception or a specific request, I work with a white porcelain as in the 19th century and not with a porcelain dyed in the mass as some current products are made.
On this white porcelain I apply pigments diluted with mediums. After each colour deposited I do a cooking between 700 and 800 degrees.
Skin colour then cheeks, eyelashes, eyebrows, mouth… so there may be 4, 5 or more successive firings.
The most delicate part is to take into account, when I paint, variations in colour as I cook.
5. The finish
On the finished head, I place the blown glass eyes, identical to the old eyes, I fix it on a body that I make, in replica of the manufacturer’s model with a composition based on papier mâché (consistency of wood) sometimes with turned wooden parts and in respect of the memory of the past (no modern materials).
Finally, I place a cork or cardboard cap on the top of the head. On this cap will be fixed a wig made of natural hair or mohair.
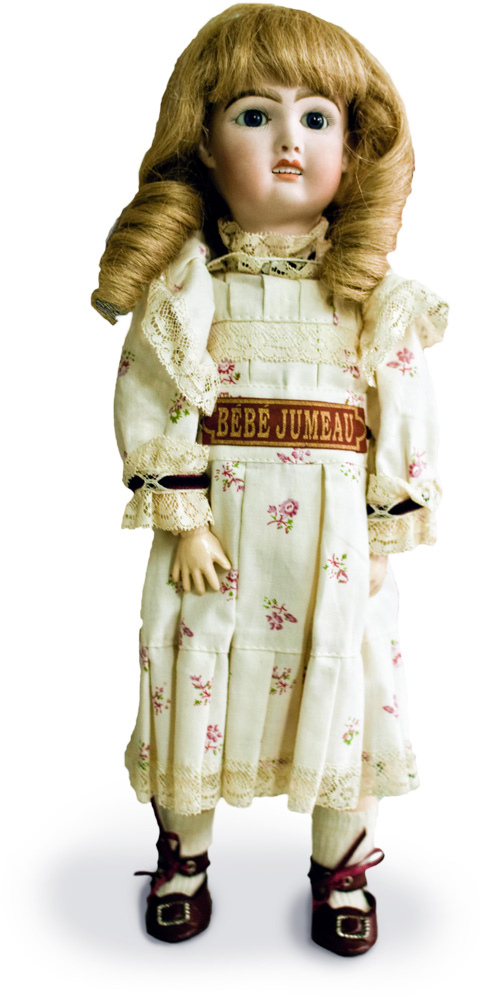
Doll reproduction
All my products are sold either bare, or dressed, or only with certain accessories: pedestal, leather shoes, underwear….
The available dolls are presented on my eBay shop and displayed in the workshop.
You can compose a doll according to your wishes.
For example: a doll with a different eye colour, another wig or clothes seen on another doll.
Dolls & spare parts
Sale available at the workshop & online
My core business is the restoration of antique dolls. In addition, I make reproductions and supply spare parts (heads, hands, eyes, body, clothes, etc.).
For more information, feel free to contact me or visit my shop directly on eBay.
Shop
Workshop
Rue de la Scierie
Nantey
39160 VAL ÉPY
Phone
03 84 47 26 93
06 08 78 20 77